Project Smart Enters Concept Gateway Phase
Why Gateway Project Management? To provide structure for Project Smart, we’ve elected to use the Gateway project management framework – a proven structure used by major OEMs to manage vehicle programmes. Originally developed in the USA, the framework provides a phased approach to manage complex projects through every phase of development. By following the same robust process as our OEM customers, we’re ensuring Project Smart is well structured from the outset. Key Gateway Stages What happens in the Concept gateway phase? This key first phase enables us to lock in the vehicle concept, fully understand cost implications and confirm funding for the next delivery stage. Our current priorities include: Identifying critical vehicle components - including optimal motor and battery solutions Designing the core vehicle architecture to integrate with our diagnostics and future features Engaging UK-based supply partners who share our quality, accreditation, and collaboration values Exploring opportunities for innovation and grant funding Meet EVie – a work in progress Thanks to our LinkedIn community poll, our project car now has a name – meet EVie! EVie has now passed her MOT and is rocking a new set of tyres. Next up we’re getting her taxed and road ready for powertrain benchmarking over the summer. What’s next for Project Smart? There’s plenty on the blocks for the project team right now, including: Finalising the engineering concept Confirming our first supplier partnerships Collecting baseline performance data Benchmarking diagnostic tools and safety systems Finalising funding and plans ready for the delivery phase Mapping out future features Keep up to date with Project Smart - We’ll be keeping our community updated online as EVie develops - follow us on LinkedIn. Interested in collaborating? We’ve lots in store for EVie. If you're a potential supplier, partner or interested collaborator, we’d love to hear from you - get in touch at [email protected].
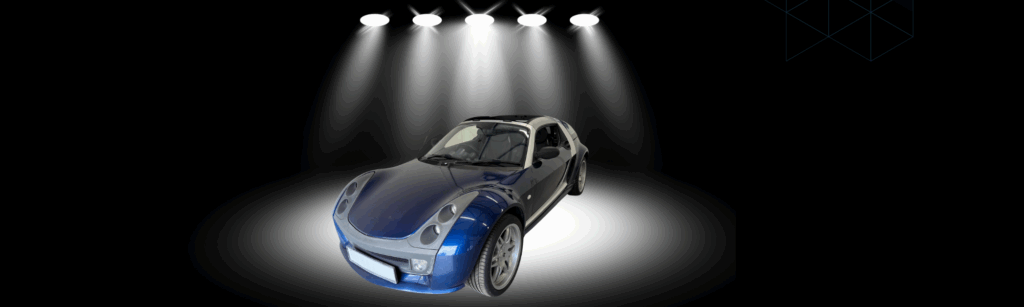
Introducing ‘Project Smart’
LRW Director Craig Fraser gives us the lowdown on what Project Smart is all about. What exactly is Project Smart? It’s our new in-house R&D project. Essentially, we’re taking a 2004 petrol Smart Roadster and converting it into a full battery electric vehicle to showcase the very latest in technology. Why Project Smart? There are four key objectives for us: To trial and demonstrate new technology To build team identity and common purpose To create a live training environment To showcase our expertise We’re also looking to build some new relationships with businesses who want to get involved and, of course, have some fun with the car as a team! What made LRW choose to develop a Smart Roadster? It’s a vehicle that we had available as a project car, so it made sense from a sustainability and cost standpoint. We also want to see just what's possible when you electrify a lightweight, relatively simple car - a stark contrast to many of the highly complex artworks that we work on day to day. It’s also a fun little car and ripe for conversion! What kind of technical workstreams have you got in mind? There are lots of ideas on the table right now! Everything from OBD (ZEVonUDS), through core software development, prognostics, battery maintainability and predictability, to using novel materials. Can other businesses get involved? Absolutely. We’re particularly looking for companies we can collaborate with on grant funding opportunities, and we’re interested in hearing from OEM partners, as well as hardware and software providers. The project offers a great opportunity for R&D collaboration and means we can showcase product capability in a real-world application. Plus, there should be some great joint marketing opportunities. Finally, anything fun planned with the car? Of course! We’re looking at lots of options - including getting the car out on the road regularly as well as events such as hill climbs. We want the automotive community to get involved in the project, so keep an eye on our LinkedIn for more on that. We’re also planning on producing lots of content around the car development – including YouTube videos. To keep track of Project Smart developments, follow LRW on LinkedIn. To find out more or get involved, please get in touch at [email protected].
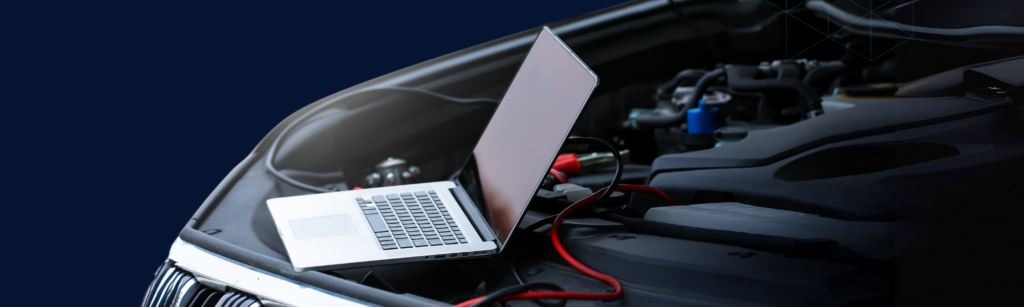
Overcoming the Challenges of Production Vehicle Evaluation (PVE) Testing
What is PVE testing? PVE testing plays a key role in verifying that fault detection, emissions controls, and monitoring systems function correctly before vehicles reach customers. It verifies whether a vehicle’s diagnostic and emissions systems perform correctly in real-world conditions. It also helps manufacturers verify that diagnostic trouble codes (DTCs) are correctly identified and reported within compliance frameworks. The process typically involves: PVE1 – Standardised Verification: Confirms that the vehicle’s meets standardised requirements for OBD functionality PVE2 – Monitoring Requirements Verification: Ensures the system correctly detects and flags specific faults and conditions PVE3 – In-Use Monitoring Performance Verification: Evaluates the performance of OBD systems during real-world driving conditions Challenges of in-house PVE testing While some manufacturers handle PVE testing internally, it can present some challenges. The process is highly detailed, repetitive, and requires specialist expertise - challenges include: Sits outside of production workflows - PVE testing is not a continuous process, so it doesn't always align with existing workflows which can make it difficult to schedule Requires specialist skills - Successful testing requires personnel with a precise, detail-oriented mindset—it is a highly technical yet repetitive task Fault detection complexity - Vehicles can generate 400 to 500 DTCs, each must be checked, categorised, and reported correctly. Some faults are particularly complex and require real-time driving conditions and deep vehicle system knowledge Data reporting requirements - Each fault must be tested under specific conditions and data must be reported in a compliant format that meets industry standards Reasons to consider outsourcing PVE By outsourcing PVE testing, manufacturers gain access to specialist expertise and optimised processes, as well as independent validation. Key benefits include: Increased efficiency and cost control - testing can be performed in a cost-efficient way. Testing can be carried out on chassis dynamometers (dynos) or highways, optimising the use of dynos only when necessary Access to expertise and proven methodologies - third-party testers typically work across multiple manufacturers and have refined testing methodologies to drive efficiencies Objective validation – independent testing demonstrates best working practices and ensures an unbiased assessment of results Streamlined data management and reporting - PVE generates large datasets. Good outsource providers should provide structured, digestible data to aid decision-making The LRW approach ‘We’re finding demand for PVE support is high right now. Our customers use us because of our experience as well as our proven methodology and mindset. Where we add real value is our understanding of system applications which means we can think outside the box to resolve issues. We take ownership of any problems identified and can tailor the fault insertion method to get the required result. With PVE the devil is definitely in the detail! Given the volume of data generated in PVE testing, we ensure that we provide quality data to our clients in an efficient and digestible format - with hyperlinked documentation and summarised insights.’ Richard Threlfall, Director, LRW Engineering Associates. Looking for PVE support? Our expert team work on PVE work packages for several leading automotive manufacturers. To find out more, please get in touch at [email protected]
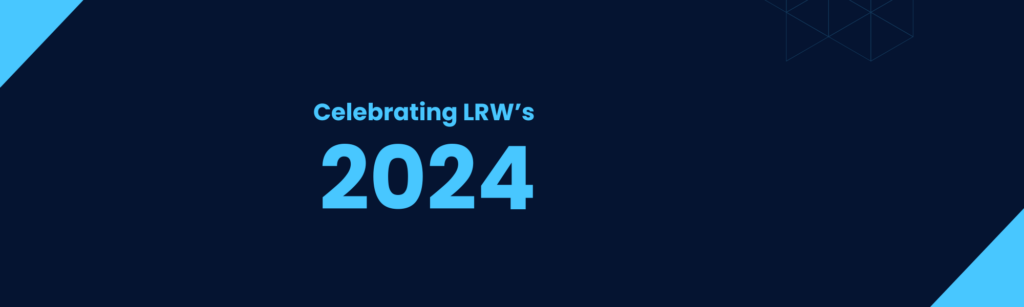
Celebrating Team LRW’s 2024: a year of growth, investment and expansion
Thanks to the hard work of the entire team, last year was really successful for us - marked by securing top talent, expanding our client base and investing in upskilling our people. All of which puts us in a great place for the year ahead. Here are my 2024 highlights: Team growth We welcomed five new engineers to LRW, whilst retaining our existing talent, ensuring we have the right expertise as we move into 2025. We also secured ex-Aston Martin John McLean as our new Programme Director who started with us this January. New clients and expanding partnerships 2024 was a year of growth, not just in our projects and team, but also in our client base. The relationships we built meant that we took on more projects for existing clients, brought on new clients and also developed existing partnerships - including Influx Technology and Warwick Control Technologies. Consistent delivery Thanks to the team’s dedication, we consistently delivered client projects, on time and on budget. We’ve been at the forefront of cutting-edge projects, working on everything from contributing to hypercar IVAs (individual vehicle approvals), ION detection, PVE (production vehicle evaluation) testing, through to fuel cell development for hydrogen buses. Increase in PHEV, BEV and new energy projects We saw a marked step up in new energy projects as the shift toward electrification continues. With even more PHEV and BEV projects under our belt, we’ve deepened our expertise in hybrid technology and new energy, including the latest OBD standards for EVs such as ZEVonUDS. Training and development investment Continuous learning is key for us to continue to deliver the best possible service for our clients. Our people have embraced training opportunities, and we expanded our in-house skillsets in: Functional Safety ISO 26262 Advanced controls and integration CAN We’ve already had a strong start to 2025 and I'm excited for the year ahead. There’s lots to look forward to - including expanding our support for low volume and niche manufacturers. So, a big thanks to the whole team and here's to a brilliant 2025! Craig Fraser, Director. Need engineering support in 2025? Get in touch with the team on 01908 110 997.
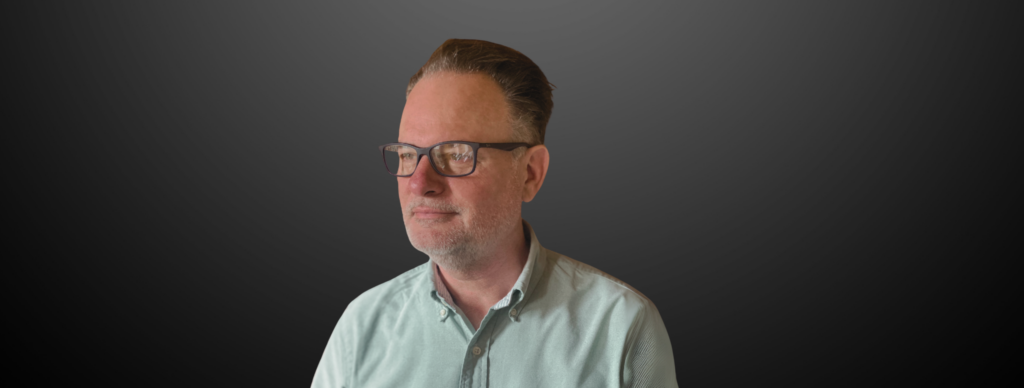
Aston Martin’s Head of Powertrain Software and Calibration joins LRW
John will be responsible for strategic project and technical oversight, leadership of cross-functional teams as well as compliance and quality assurance. John brings over 35 years of powertrain and controls experience including, most recently, 18 years at Aston Martin. Prior to Aston Martin, John held roles at Rover Group, Tickford Engineering, Prodrive, and Ricardo. Whilst at Aston Martin, John headed up the calibration department and was responsible for more than 50 software and calibration engineers across the UK and Germany. John grew the department substantially during his tenure - when he began leading the calibration team in 2006 it totalled just six engineers. Over almost two decades with the prestige manufacturer, John was responsible for introducing the Bosch engine management system, leading the development of the controls platform for Aston Martin’s engines and transmissions, as well as the first hybrid controls application for the Valkyrie hypercar. Richard Threlfall, Director for LRW, commented on John’s appointment: ‘We’re delighted to welcome John to LRW. John’s appointment is a key part of our business growth plan, and we’re excited about what he will bring to the team. We’ll be harnessing his wealth of calibration experience to support our clients, and he will also be invaluable in helping us to further develop our engineering talent.’ John explains what drew him to LRW: ‘I was looking for a new challenge and was aware of LRW through my time at Aston Martin. I like the fact that LRW is a smaller, growing British company with a great delivery track record. I’m particularly passionate about making a tangible difference by supporting the brilliant and hugely enthusiastic engineering team. The other key draw for me was the work LRW are doing in the future tech and new energy space. I’m excited about the fresh challenge and getting stuck in.’ John joins the LRW team on the 27th of January. Need expert engineering support? Get in touch with the team on 01908 110 997. Keep in touch by following us on LinkedIn.
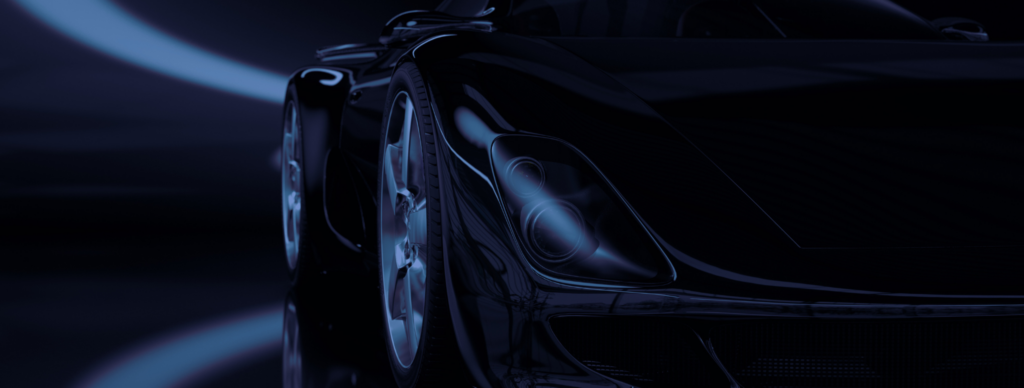
Why team LRW has a passion for low volume and niche manufacturing
We get the view from John Veevers, Senior Calibration Engineer, on why the team are so passionate about supporting the sector. What can LRW offer to niche and low volume manufacturers? Our team has an incredible back catalogue of working with, and for, some of the most exciting automotive manufacturers out there. That means we can bring our engineering expertise to support smaller manufacturers. Our skillset spans OBD calibration, testing, certification and validation as well as control systems, toolsets and software design. We also work with suppliers to the low volume industry. How do you work with smaller, more niche clients? We’re extremely flexible. We can work on or offsite with our clients and integrate closely with their existing teams. Because we’re a smaller business ourselves, we’re nimble and can deploy our engineers quickly. LRW understands how important this is for rapidly evolving niche projects and businesses. What makes the team so passionate about low volume? As well as having the sharpest set of engineering brains I think I’ve ever worked with, many of the team are genuinely obsessed with cars and modern powertrain technologies, but we all have our iconic favourites of the past! There is a shared passion here for innovative and unique projects. Most of us will happily spend our downtime working on our own vehicles – there’s a lot of petrol running through our veins. Sounds like you’re speaking from experience John? Absolutely! I built my first car at 17 from a pair of non-running Mk 1 Volkswagen Golfs. I also created the first Toyota Supra with a fully integrated Lexus LS400 Electrical Architecture, including fully functional powertrain, chassis, body and comfort systems. And, two decades on – via stints including JLR, PalmerSport, Hedley Studios and Rolls Royce Bespoke - I’m still excited about every new project! Want to find out more about how LRW can help? If you need expert support with your next low volume or niche vehicle project, please give us a call on 01908 110997 or drop us a line at [email protected].
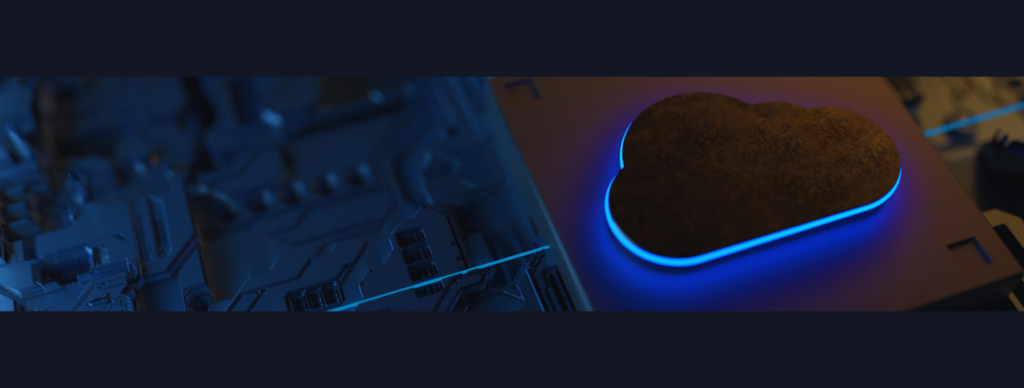
LRW to launch ShieldStream telematics solution at international marine show
LRW Engineering Associates is debuting its marine telematics solution ShieldStream at the METS Trade show in Amsterdam later this month. The new ShieldStream solution securely feeds live data to the Cloud which can be accessed from anywhere. It is CAN NMEA 2000 enabled, includes configurable alerts and is available as plug and play or with bespoke configuration support. Two ShieldStream Pro versions are also available: ShieldStream Battery Pro - adds battery data management to the core solution and supports all EU battery passport requirements, which will be mandated from 2027 ShieldStream Cyber Pro - includes security capability and network prognostics ShieldStream has applications across the marine sector - from individual boat owners, through to marine fleets and ship builders as well as warranty and insurance providers. LRW Engineering Associates Director and New Energy and Integration Lead, Richard Threlfall commented: ‘We’re really excited to be launching ShieldStream to the marine market. The solution enables users to anticipate issues such as diagnostic events or high temperatures before they become a serious problem. And that is key to improve marine reliability and efficiency. We’re also anticipating significant demand for the Pro versions including the Battery Pro which will be a key piece of kit as it handles all the battery data management which the EU is mandating from 2027.’ The LRW team will be on METS stand 03.223, joining Warwick Control Technologies - a world leader in Controller Area Network (CAN) and related technology. The exhibition runs from the 19th to the 21st of November - for more information, visit: https://www.metstrade.com/exhibition For more information on ShieldStream, visit: LRW Products Want to find out more about our work in the marine space? Get in touch on [email protected]. Posted: November 2024
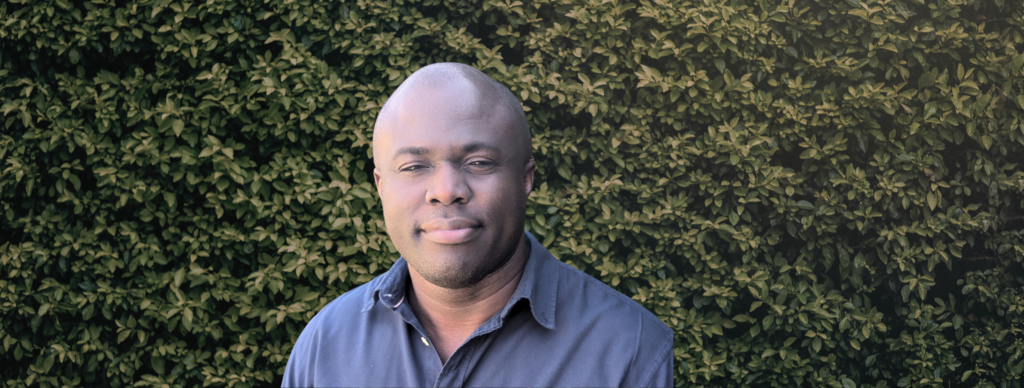
Meet the team: Cobbinah Paha – LRW’s new Senior Controls Engineer
How did you get into automotive engineering? I studied five years of physics and one of applied engineering at University in Germany. When I moved to the UK, it was tough to find a job in pure physics, so I joined Ford working on design calibration for engines. What’s your career history? I spent four years at Ford and worked my way up to Powertrain Programme Team Leader. From Ford, I went to Caterpillar as a Validation Engineer working on engine reliability, analysis and assessing design weakness. I wanted a numerical based role and that led me to a model-based engineering role at Tantalum Innovations working on reverse data engineering for fleet telematics. Then a stint at TAE in Birmingham gave me a real interest in battery management systems. I found out just how much physics and engineering goes into it, which gave me a newfound respect for an AA battery! Most recently, I was at Intertek Transport Technologies as Principal Controls Engineer working on engine controls and communication protocols - including testing for electric motors. Greatest career achievement to date? Designing a fuel usage prediction model for fleets which is now used as the default for the industry. What made you apply for the role at the LRW? I was aware of the LRW position as my previous line manager knew LRW Director Richard Threlfall. Because of that, Richard understood my skillset which made the interview the most unconventional I’ve ever had – in the pub! Richard knew I had the expertise that LRW was looking for, so he was more interested in me as a person and ascertaining whether our technical thinking would align. What projects have you worked on at LRW so far? I’ve worked on three different projects to date. Initially I designed test scripts to support the calibration team for a hyper car project and I’ve built controls models for a hydrogen-electric aircraft project. Currently, I’m working on a special project using multiple scripting languages to develop a unique communication algorithm. Plus, I support the team with my ‘side hustle’ of any scripting jobs. How are you finding it so far? I’m enjoying it! I love the controls side of engines – it’s all about the data for me and teasing information out of groups of numbers to enable valuable knowledge transfer to other people. The fuel cell work is also really interesting. And what's it like working with the LRW team? The team are real experts but humble too. I like working with a smaller team as you get to work across different projects, it’s challenging and keeps you on your toes. I’m also enjoying working with our talented graduate engineers and being able to exchange knowledge with them. What’s your working pattern? It’s hybrid. Typically, I’m at home three days a week with the rest in the office for face-to-face team interaction plus some client visits. Are you a petrol head or indeed an electric head? No! I’ve never been interested in cars – so no Ferrari for me! When I look at automotive, I see arithmetic – it’s always been about working with numbers for me. Hidden talent I’m a resource research driven guy and I enjoy being thrown in at the deep end - I lean on physics, that’s my hidden toolset. And outside of work? I used to play tennis, but I now have two small boys under three, so the racket is hung for now!
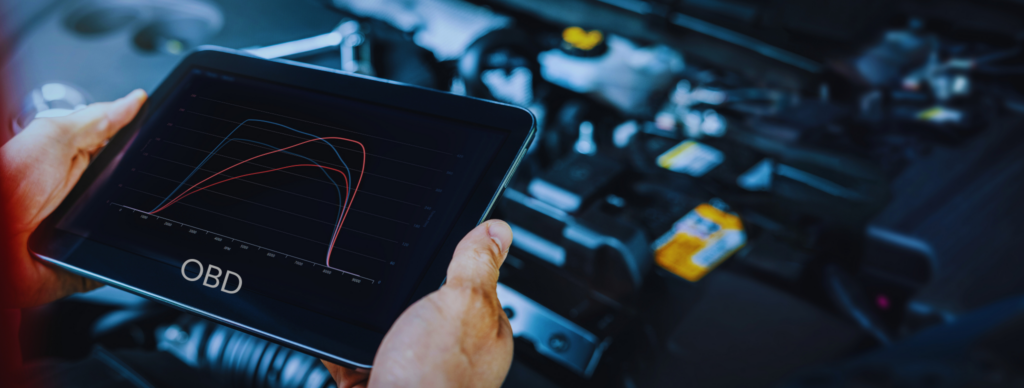
OBDonUDS – An evolution of OBD
What is SAE J1979? Also known as “OBD Classic” protocol, this is the standard that covers the current communication between the vehicle’s OBD systems and test equipment. What’s changing? A new protocol is being legislated, SAE J1979-2, also known as OBDonUDS (Unified Diagnostics Services). OBDonUDS is being brought in to improve and expand vehicle diagnostics data to better handle the increased complexity of modern vehicles. Who introduced the changes? The updated standard has been introduced after extensive discussions with members of the global engineering organisation SAE International in conjunction with CARB (Californian Air Resources Board). Why will OBDonUDS be better? OBDonUDS is not just a translation of the classic SAE J1979 services to UDS services, it provides extra features to enhance diagnostic accuracy. It will help to better pinpoint diagnostic issues and provide more data around diagnostic events to ensure quicker and more accurate resolution. What differences are there with OBDonUDS? It uses UDS – UDS is an established standard which provides a consistent, flexible and secure framework for diagnostic communication 3 Byte Diagnostic Trouble Codes (DTCs) vs 2 in OBD Classic – this will provide more (and much needed) unique DTC definitions Extended data records for DTCs which will provide better fault diagnosis Increased information on individual OBD monitors - including completion and how often monitoring occurred in–use More snapshots of engine and vehicle operation conditions when emissions related malfunctions are detected – it supports snapshots for up to five DTCs and two occurrences each DTC based readiness to monitor the vehicle’s self-test of emission control systems Readiness group to DTC readiness translation to relate fault checks to particular systems What is the timing for the phase-in of OBDonUDS? In the US market OBDonUDS will be mandatory for all vehicles sold from model year 2027 (from the 1st of January 2027) to comply with the new standard. During the phase-in period, Classic OBD or OBDonUDS can be used for model year 2023 up until the 2027 deadline. What are the implications for diagnostics? New SW development in OBD relevant modules is needed to support OBDonUDS New validation procedures are required to test the OBD portion of the ECU software More information broadcast which needs to be validated for accuracy What’s the LRW view? ‘This is a critical change in diagnostics and we believe it will be really positive. Having more DTCs and additional freeze frame data will be useful in supporting quicker and more accurate vehicle fault diagnosis. Ultimately that will improve repair times and the experience for the end customer. We are actively developing this on vehicles now to ensure our clients are ready for the 2027 deadline.’ Craig Fraser, LRW Engineering Associates Director and Diagnostics Lead How to map common fault codes from OBD to OBDonUDS Are there plans for enhanced OBD standards for electric vehicles? Yes. There is a further iteration J1979 standard for Zero Emissions Vehicles SAE J1979-3 ZEVonUDS. The ZEVonUDS SAE J1979-3 standard introduces on-board diagnostics (OBD) also for electric vehicles / Zero Emission Vehicles (ZEVs) and Plug-in Hybrid Electric Vehicles (PHEVs). Want to find out more? Here are some useful links: SAE International Standards 1979-2 Vector OBDonUDS video Need some help? The LRW team is made up of specialist engineers, we work on cutting edge diagnostics projects for leading automotive manufacturers. To find out more, please get in touch at [email protected].
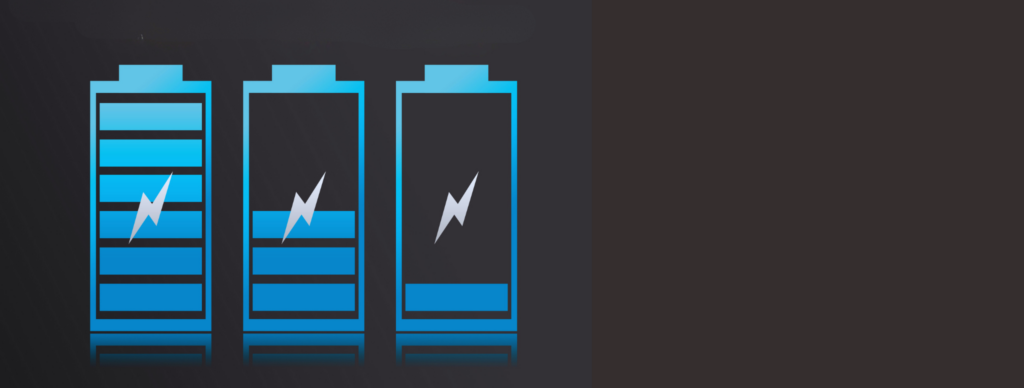
Why battery passports are critical to mass electric vehicle adoption
The path to zero emission vehicles The sale of new internal combustion engine vehicles (ICE) is expected to be banned in the UK by either 2030 or 2035 - dependent on whether the new government reverses the 2035 extension implemented by the Sunak administration. The current Zero Emission Vehicle (ZEV) mandate dictates that 80% of new cars and 70% of new vans sold in the UK must be zero emission by 2030, rising to 100% by 2035 ¹. Lack of EV battery confidence is a key barrier in EV adoption As the number of electric vehicles rise, so too does the number of lithium-ion batteries in use. Even though many manufacturers offer an eight year or 100,000-mile battery warranty, lack of market confidence means that the EV battery remains an obstacle to widespread EV adoption. What are the impacts of low market confidence in EV batteries? Concerns around EV batteries have wide ranging market impacts including: Struggling EV retail sales - consumer concern that the battery will need replacing at an excessive cost is contributing to a lack of retail market confidence in EVs. New EV market sales are predominantly driven by business and fleet Negative impact on EV used sales – a survey by the Green Finance Institute found that 62% of drivers who don’t already own an EV said concerns around battery lifespan was a reason they would not buy a used EV ² Uncertain residual values impacting lease costs – battery life is an expensive unknown which is impacting residual values (RVs). This was described by the British Vehicle Rental and Leasing Association (BVRLA) in July as an ‘existential threat’ to the industry ³ Fleet operator concerns – uncertain EV residual RVs are impacting leasing costs for fleet operators. The ability to offer second or third life leases is also affected by uncertainty around long term battery health High insurance costs – insurers remain nervous about the high cost of battery replacements which contributes to EV insurance premiums typically being more expensive than ICE vehicles Richard Threlfall, LRW Engineering Associates Director and New Energy and Integration Lead, explains the importance of battery passports: ‘Right now, the battery in an electric vehicle represents a real unknown – for insurers, consumers, fleets, lease providers and the used market. Finding a way to provide reassurance will undoubtedly have a significant impact on wider market EV adoption and accelerate the journey to zero emission transport. My view is that battery passports are absolutely critical to the future success of electric vehicles.’ What does the future hold for battery passports and health checks? Battery passports - From 1st February 2027, the European Union will legislate that an electric battery passport is mandatory for all EV and industrial batteries over 2 kWH sold into the EU market. This will also apply to vehicles sold in the UK 4. Manufacturers will be responsible for supplying the passport which will include information on the battery’s lifecycle, carbon footprint, production process and transportation of the vehicle and its parts. Battery health certification scheme – A scheme, similar to those already in place in countries including Norway, is being considered for used EV batteries. The United Nations is also working on global technical regulation for EV batteries (GTR 22) which will require new EVs to include an easily accessible battery state of health monitor. Work to date is encouraging. Providing transparent, standardised information on the initial providence and ongoing used state of battery health will be critical to mass EV adoption and more sustainable transport. Find out more The LRW team is made up of specialist engineers. We are experts in what we do – we work on cutting edge electric, hybrid, and hydrogen projects across automotive, marine and aviation applications. To find out more, please get in touch at [email protected]. Sources * EV numbers: UK stats Zapmap EV stats Global stats: Our world in data - EV sales ¹ Gov.UK: Pathway to zero emission vehicle transition becomes law ² Green Finance Institute: Used EV report ³ Fleet News: Collapsing BEV values pose ‘existential threat’ to leasing industry 4 RAC: New battery passport set to impact EV market in the UK
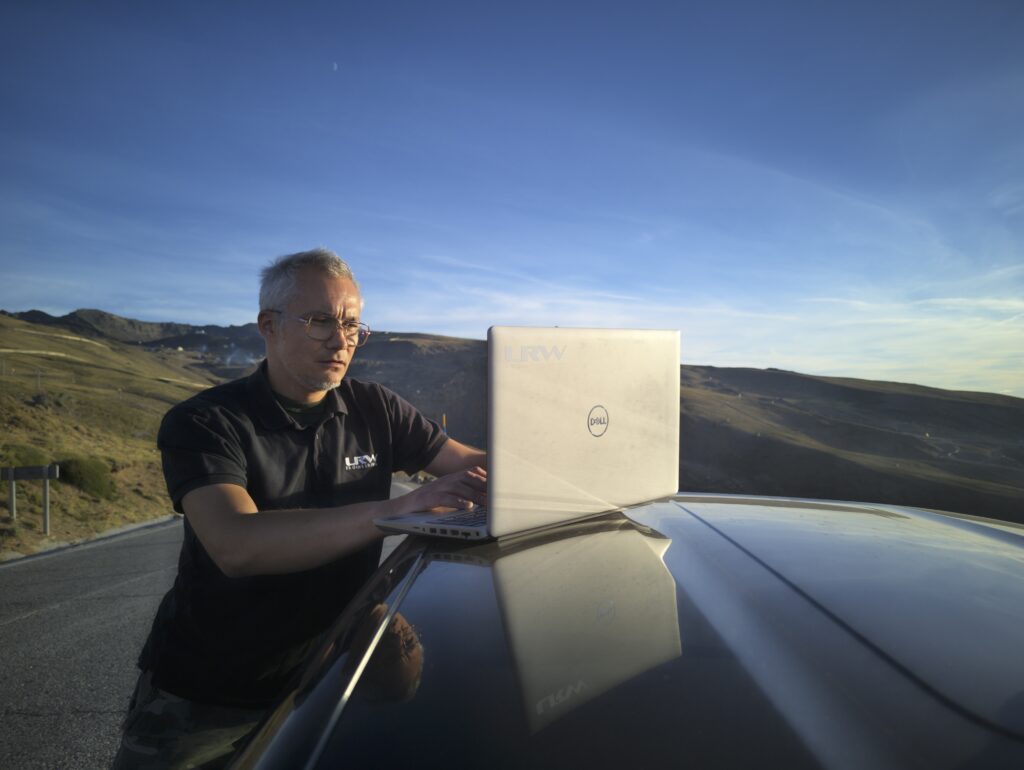
Meet the team: Kristof Pawluc
What’s your background? I’m from Poland which is where I did a masters in automotive engineering, specialising in power and performance. I came to the UK to learn English. As soon as I arrived, back in 2004, I knew the petrolhead culture suited me - the British race everything, it doesn’t even need to have wheels! When did you start working with LRW? I’ve been working with the team for two years as a regular contractor, but I’ve known the LRW guys since 2011 when I was at JLR. Tell us about your career I have 20 years of automotive experience. I started out as a vehicle technician then worked as a race engineer, sports car technician and application engineer. I was also Senior Calibration Engineer at JLR for eight years. I’m very lucky to have worked at many consultancies and facilities – and I’ve driven on many different proving and test tracks. So, what’s it like working with LRW? I can honestly say that LRW are the best in the business – and not just because they pay me! LRW works with the best OEMs and the projects are very varied and highly technical. I principally work on calibration and powertrain projects with a fairly equal split of desktop work and technical vehicle preparation, plus some testing. Because of my experience, I get to work on and drive some of the world’s most exciting and special cars. When I’m working with LRW, I honestly can’t wait to go to work! What are team LRW like to work with? The passion in the team and quality of people is incredible - everyone wants to deliver. The Directors lead the business really well, look after the team and are also incredible technical experts. They’re also amazing at finding new talent. I have genuinely never seen such progress in graduates – two years with the LRW team and they’re experts – it’s comparable to 10 years in a larger company. When people come in for interview and see what LRW do, they don’t want to leave! What’s your highlight of working with LRW to date? Many things! One project that stands out is working on what, in my view, is the best driver's car in the world. It’s pure ICE 'analogue' car back to automotive roots and entirely driver focused. But I can honestly say that every project is exciting. And, quite possibly the most important question, what do you drive? Well, I am a petrolhead and drink gasoline every evening - that is my afternoon tea. So, I need classic cars in my life although it’s a never-ending project as they are never all running! I have a small workshop at home and I’ve never paid a penny to a mechanic which means I can have a few cars. I love premium German cars which combine performance and luxury - I have a classic BMW V8 but I run an efficient diesel as my daily driver. And with that, Kristof is off to test something rather special at Millbrook – doesn’t sound like a bad day at the office.
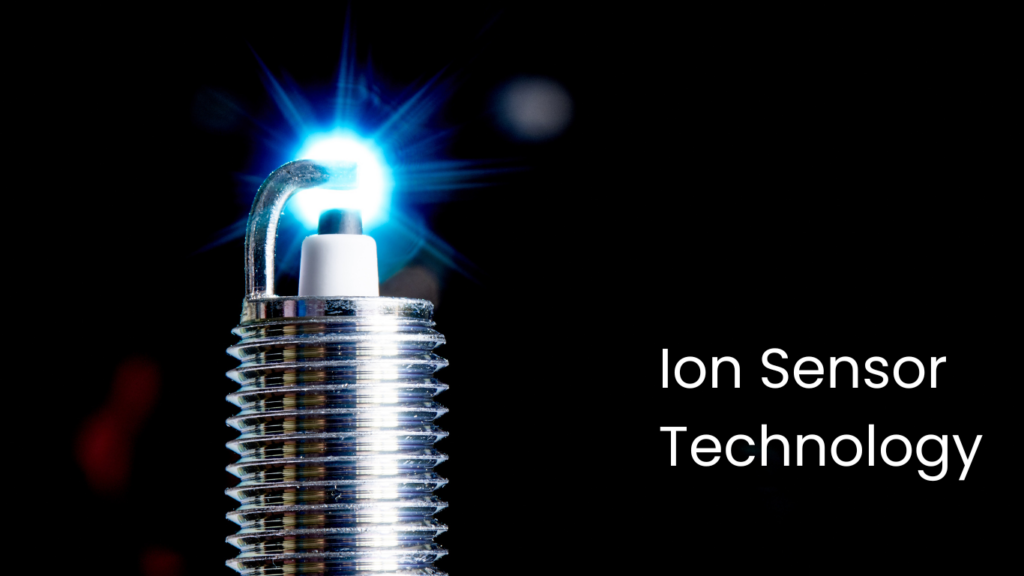
How ion sensing technology is improving automotive misfire detection
There is room for improvement in traditional methods of misfire detection – especially for engines with a high number of cylinders. And, increasingly, team LRW is seeing automotive manufacturers use a more sophisticated method of misfire detection. Enter ion sensing technology Ion sensing technology works via a sensor in the combustion chamber which can detect ions (charged particles) which are created when combustion occurs. The sensor detects the number and pattern of ions during combustion which allows it to identify any misfiring in an individual cylinder - rather than looking for a blip in the engine speed. What are the benefits? The innovative technology is expensive but more robust than more traditional methodology, benefits include: No false passing or false detection Diagnostics work better and provide improved results Excellent for high cylinder engines such as V12s Early detection compared to methods reliant on engine response Cylinder specific data – each spark plug provides data for its specific cylinder making it possible to identify the misfiring cylinder Dr Steven Higginson, LRW Engineering Associates Director and Calibration and Controls Testing lead, explains how the technology is working in practice: ‘Ion sensing technology is the way forwards for misfire diagnosis on engines with multiple cylinders. The technology is costly right now, but I’m pleased to say that some vehicle manufacturers are embracing it and we’re really seeing the value in how it performs. We’ve used the technology on a couple of client projects so far and we’re integrating it into client’s applications with excellent results.’ How LRW can help Our engineers are highly experienced in working with manufacturers on specialist diagnostic and calibration projects. To find out more, please get in touch at [email protected].
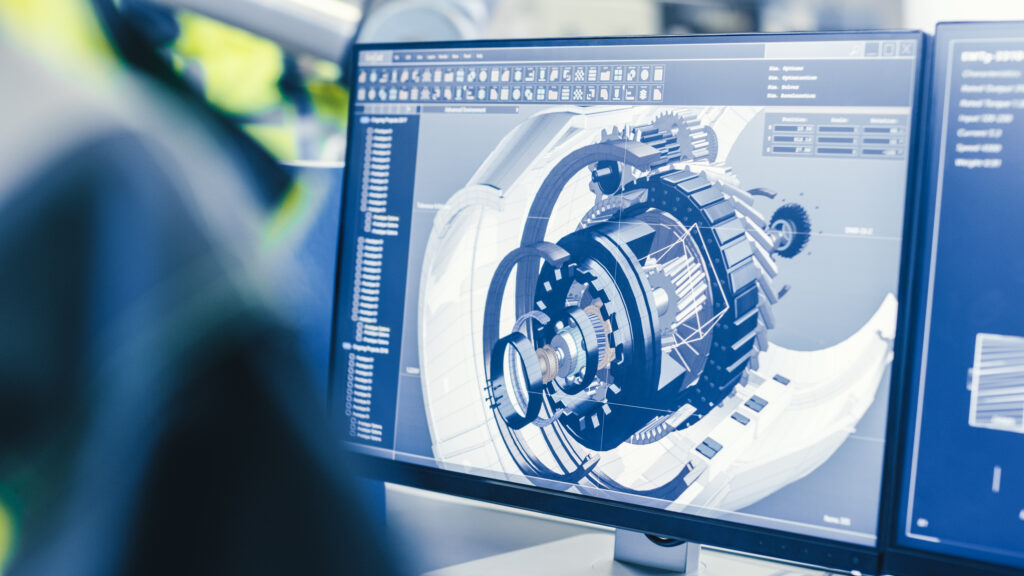
How Powertrain in the Loop is accelerating early-stage development for automotive engineering
HiL is a growing technology and has a global market value predicted to reach 2,230 million dollars by 2032 - according to GlobeNewswire. So, what is PiL and why is it such a useful engineering technology? What comprises a typical PiL set up? Typically, a PiL set up includes the engine, transmission and drivelines. Everything else is simulated – from the accelerator pedal to the ambient conditions. This allows engineers to isolate the key components they are interested in. What is PiL useful for? PiL is particularly useful to enable front load development work before new vehicles go into production. It is particularly useful for: Early diagnostic calibration development Running emission cycles Fault simulation testing LRW Engineering Associates Director and Calibration and Controls Testing lead, Dr Steven Higginson, says that PiL can really accelerate early-stage validation: ‘Powertrain in the Loop is a highly valuable tool for accelerating early-stage vehicle development. Being able to force cool the system saves a lot of time during testing and helps significantly speed up test programmes and validation.' Key benefits Repeatability – ability to have the same inputs or simulate different inputs consistently Calibration development can be front loaded prior to a development vehicle being required Faster results Ability to simulate worst case drive cycles or manoeuvres without the risk and expense of vehicle prototype damage Possible to simulate ambient conditions – including temperatures and pressures How LRW can help Our engineers are highly experienced in working with OEMs on proprietary PiL set ups and use their know-how to ensure the best possible project outcomes. If you need support with HiL or PiL projects, please get in touch at [email protected].
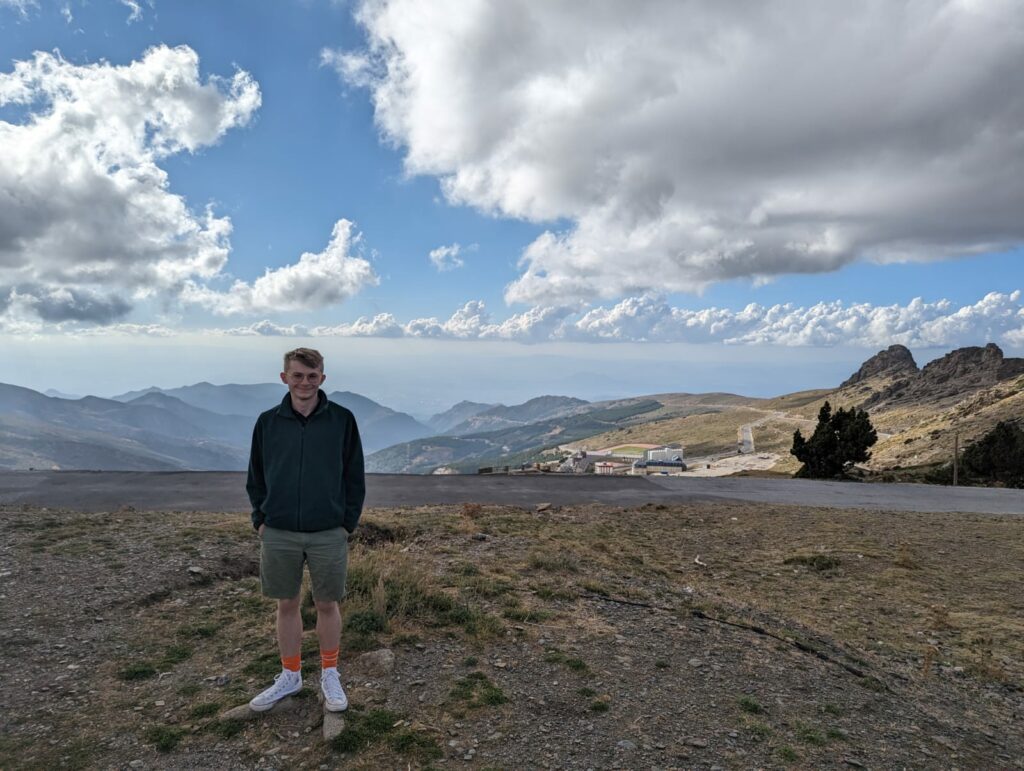
What’s it really like to work at LRW Engineering Associates?
When did you join LRW? In 2022, I joined straight from University with a degree in Mechanical Engineering, with control systems. What made you apply for the role? The Calibration Engineer role combined all the facets of engineering that I really enjoyed at University, so that was a big draw for me. I also wanted to work somewhere where I was really connected to the end product and could get involved with meaningful projects. What’s it like to work at LRW? I feel very privileged to be part of the team here, they’re a great bunch of people and have a real wealth of experience. I’ve learnt so much in the last 18 months and I feel I’m way beyond where I would be working in a larger company. I have to say that I’m not a petrol head, but it doesn’t get any better than the engineering projects we work on at LRW. We work with the best of the best – some of the luxury cars are actual works of art! So, what does your role involve day to day? Typically, I’m in the workshop but it is varied, we might be on site with a client and there is also the flexibility for some home working. Every day is different but normally my role is a combination of desk work – data analysis and processing - plus more physical hands-on work on the vehicles. Best thing about LRW? Being master of my own destiny. I’m in charge of a package of work and I see it through from the start to the end, that’s really satisfying. Plus, the projects are genuinely interesting and there is always something new to work on. Highlight of the role so far? My first heat testing trip last year was pretty phenomenal. It was a brilliant experience to be part of a global community of engineers and I learnt a huge amount. What do you drive? A bicycle! I love cycling and that’s how I get to work. Hidden talent Currently learning Cantonese.
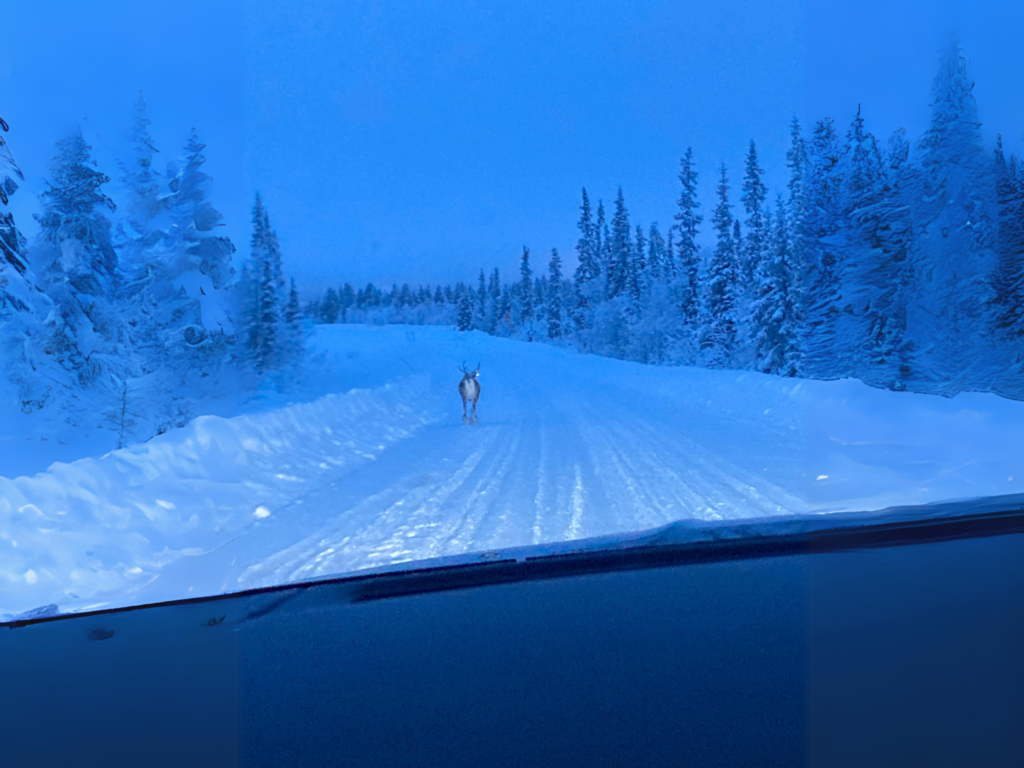
Reindeer ahoy – it’s cold testing time for team LRW
Last year we carried out heat environmental testing and hot altitude testing for a luxury sports car manufacturer client. For this trip, it was time to layer up and get the cold environmental testing (CET) done. How we cold tested LRW offers CET as part of its range of testing services. Ensuring new vehicles perform in all environmental conditions – including extreme cold - is critical for OEMs creating prototypes. The vehicles were run through the LRW standard test and validation plan, to ensure that the diagnostics (including emission control) work nominally at extreme cold temperatures - right down to -30. We also tested the vehicles when cold soaked, which enabled us to assess the warm-up profile. So just how cold did it get? Steven explains: ‘It was pretty cold! We saw temperatures of -30 on the trip and got a big dump of snow which gave us ideal testing temperatures of between -20 and -30. We’re looking for how rational the sensors are in these extreme conditions and checking for plausible behaviour in the car. It’s a phenomenal experience – Kiruna is on land owned by the Sámi people so they’re herding thousands of reindeer on Ski-doos. I have to say the reindeer are seriously imposing, and when you’re driving a luxury car that makes you extremely cautious!’ Why cold environmental testing? To test any new powertrain - or variant - in a cold environment Testing in a ‘real life’ field setting can be more effective than that using a climatic chamber as a broader range of road conditions and temperatures can be tested To understand the normal parameters as a standard part of the calibration testing process The LRW test team The trip test team included LRW director and senior engineer Steven Higginson and calibration engineer Danny Harding. It was Danny’s first environmental test trip with the team which he fully embraced - and it wasn’t just the cars that got tested. Steven comments: ‘Testing trips are always full on but team LRW do like to embrace the local culture in our downtime. So, with apologies to our new reindeer friends, we did try out the local speciality of reindeer pizza. Also, it turned out that the Swedish craze for the game of padel had reached even this remote frozen corner, so Danny and I were inducted into that too – which thankfully was inside.’ Trip outcome The diagnostics performed as expected and were stable in extreme cold conditions. The client feedback on team LRW has been excellent. Now thawing out, the test team are getting ready for the next cycle of heat testing later this year. Need support with environmental testing? Get in touch with the team at [email protected]
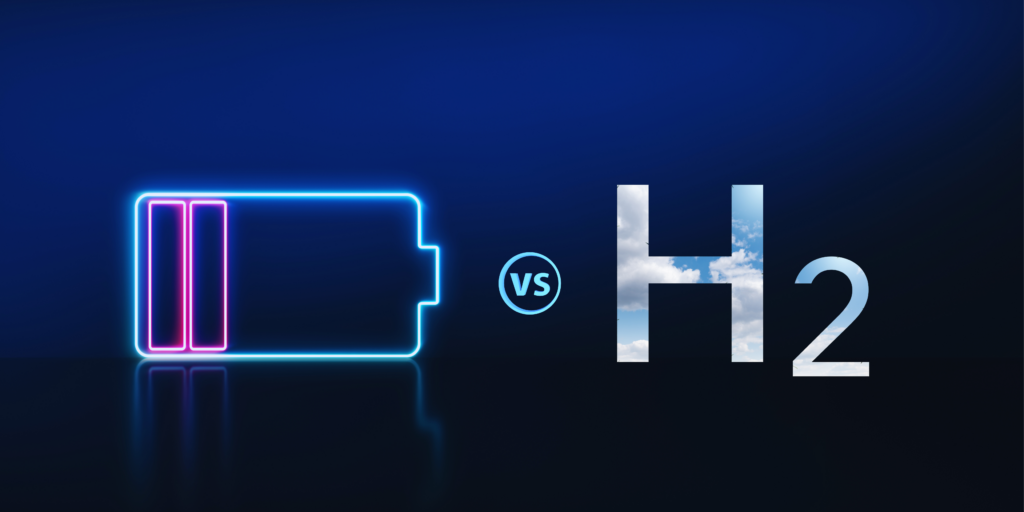
Battery vs hydrogen – why electric battery is only part of the zero-emission transport solution
LRW Engineering Associates Director and new energy and integration lead, Richard Threlfall, says that electric batteries are just one part of the answer: ‘My view is that battery is a short-term fix to a long-term problem, and it is just one part of the future of clean energy transport. It’s also important to consider hydrogen which, from an engineering perspective, I see as a more sophisticated, long-term solution. Hydrogen is obviously a very clean energy, it’s the most abundant element on the planet and a game changer in terms of range. However, it’s a more complex energy to harness so it will take longer to develop the products.’ Weighing up battery vs hydrogen Electric battery powered transport is becoming more mainstream, with almost a million fully electric cars now on the UK roads, according to Zapmap. But the current battery offering has limitations and is relatively expensive. Recharge time is slow compared with traditional refuelling, which presents a particular challenge for aviation, marine and heavy goods vehicle applications. Temperature sensitivity is also an issue as battery performance can be significant reduced in cold weather. Hydrogen offers fast refuelling and longer range with potential to be a good wider transport solution. Hydrogen fuel cells are lighter and more compact than electric batteries and offer a longer lifespan. Hydrogen cars, like the Toyota Mirai, exist today but are currently limited. However, a number of leading manufacturers - including BMW and Jaguar Land Rover - have vehicles in development. Hydrogen presents more operational challenges than battery power - not least the ability to pipe it and store it at extremely high pressure. Richard comments: ‘Hydrogen still has an image problem and people can be nervous about the safety implications of having a flammable substance onboard. The reality is that today, we think nothing of transporting a highly combustible can of petrol in our cars. The real challenge for hydrogen will be to create demand and scale production.’ But is it really clean energy? Whilst battery and hydrogen powered transport offer zero emissions, impact throughout the energy lifecycle needs to be considered. Electric batteries have a negative environmental impact due to lithium mining, the manufacturing process and end of life disposal. Hydrogen production typically produces carbon dioxide emissions, although some countries use renewable methods – Denmark uses wind energy and Iceland harnesses geothermal energy to power production. Infrastructure and investment New energy needs new infrastructure and that will require significant investment and sustained government support. The automotive electric battery charging infrastructure is growing in the UK but motorway chargers remain behind target, as reported in The Independent. For sectors such as marine and aviation, electric infrastructure is still in its infancy although it is developing with encouraging projects including marine infrastructure for the south coast and Aerovolt installing charging stations at regional airports. The challenge with hydrogen is to both store it and create specialist infrastructure to pipe it to refuelling stations. Some countries have already made good strides in this respect – FuelCellsWorks says China leads the way globally with over 400 hydrogen stations and 13,000 fuel cell vehicles, Hydrogen Insight reports that Germany is ahead in Europe with 91 stations - the UK currently has 15. Richard concludes: ‘LRW is excited to be progressing the new energy agenda. We’re working on some really exciting new energy projects right now – including the development of a hydrogen-electric powertrain for passenger aircraft and the electrification of some specialist heavy-duty transport. The good news is that we have two highly viable new energy options on the table which will ultimately drive down carbon emissions.’ Need specialist expertise support for new energy engineering projects? Get in touch on [email protected].
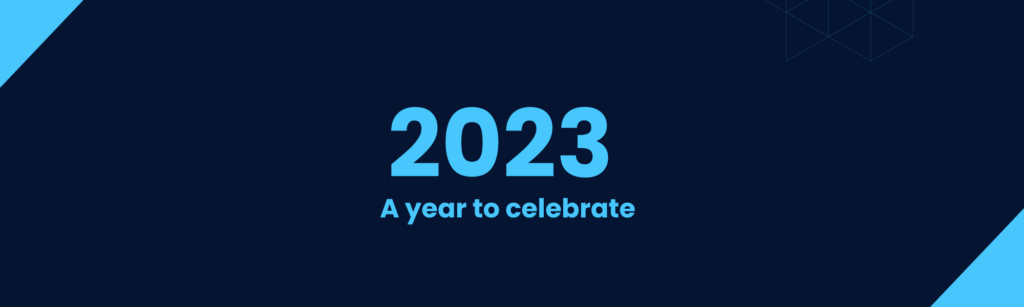
So, that was 2023 – a year to celebrate for LRW Engineering Associates!
Personally, I’ve now been with LRW for over 10 years and I’m feeling really proud of what we’ve achieved – especially over the last 12 months. It’s so important to take the time to reflect and recognise the success of our team – so, here are my top 5 reasons to celebrate LRW’s 2023: 1. The team has grown – In May we appointed Jared Al-Hilali as a Partner and Director, he brings excellent engineering credentials to the team and a career history which includes Group Lotus and Nissan. We also appointed an additional three experienced engineering heads during the year to support new contracts. 2. We’ve moved office – twice!- We’re now based at brilliant premises in Milton Keynes with excellent facilities to improve our in-house testing capabilities. It’s an ideal location with good proximity to customers and close to the UK’s regional automotive hub. 3. We’re embracing new energy projects– As the world continues to transition away from traditional fuels, we’re evolving too. This year we’ve worked on hydrogen fuel cell and zero emission aviation projects and there are more planned for the new year. 4. It’s been a good business year – We’ve seen good business growth in 2023. We’ve won new customers as well as solidifying relationships with existing customers and we’re heading into the new year with a solid new business pipeline. 5. We’ve had a marketing upgrade – this year we’ve invested in getting our marketing foundations in place. We’ve created a new website, updated our brand and materials and we’re getting more active on LinkedIn. So, it feels like we’re in a great starting place for 2024 and the LRW team are looking forward to another brilliant year ahead supporting our clients. Craig Fraser, Director. Need engineering support in 2024? Get in touch with the team on 01908 110997.
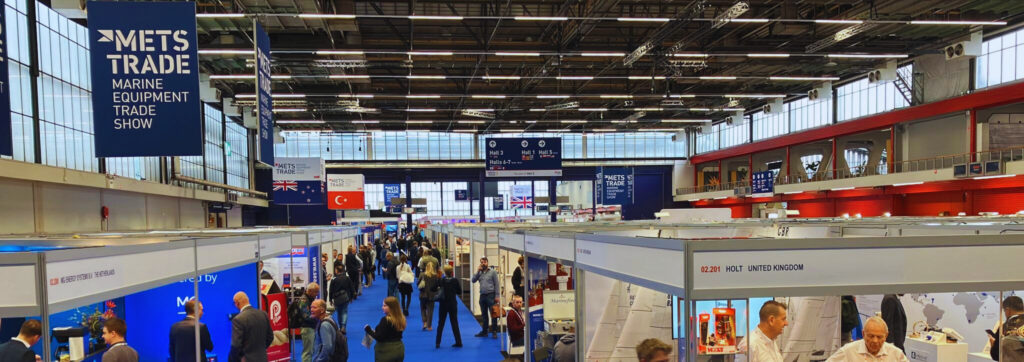
LRW Engineering Associates onboard for world’s largest marine show
LRW exhibited at the show alongside Warwick Control Technologies - a world leader in Controller Area Network (CAN) and related technology. The team were there to raise awareness of LRW’s engineering expertise in marine – including hybrid, fuel cell and safe-chemistry pure battery platforms, data and diagnostics. Richard reported an interesting and packed three-day show with an emerging focus on new energy. Richard commented: ‘Emissions are less of a focus in marine compared with what we’re seeing in automotive, but it was great to see sustainable energy solutions gathering pace. There were all sorts of weird and wonderful battery electric and hybrid solutions on show, and it was great to see sustainable solutions gaining traction. We also see real potential in hydrogen fuel cells but, because it’s a new technology, it will take time for the industry to get comfortable with it. Hydrogen is the cleanest fuel available, it’s sustainable and inexhaustible - plus it doesn’t require significant recharge time so it’s ideal for marine applications.’ The team also reported productive conversations around connected data and are exploring how LRW’s data analysis and diagnostics know-how could provide solutions for the marine industry. Richard explains: ‘We’re working on a solution to pool existing marine data, using the NMEA data protocol, into a visual dashboard to allow boat fleets to anticipate problems. This will allow better preventative management of issues such as degradation before it becomes a problem, and it could massively improve reliability and efficiency. We see better use of data in the marine space as being a real game changer.’ LRW plans to return to METS in 2024. The show organisers announced a record expo this year – the show attracted over 1,500 exhibitors and almost 19,000 visitors across the three days. For more information on METS 2024, visit: https://www.metstrade.com/exhibition Want to find out more about our work in the marine space? Get in touch on [email protected].
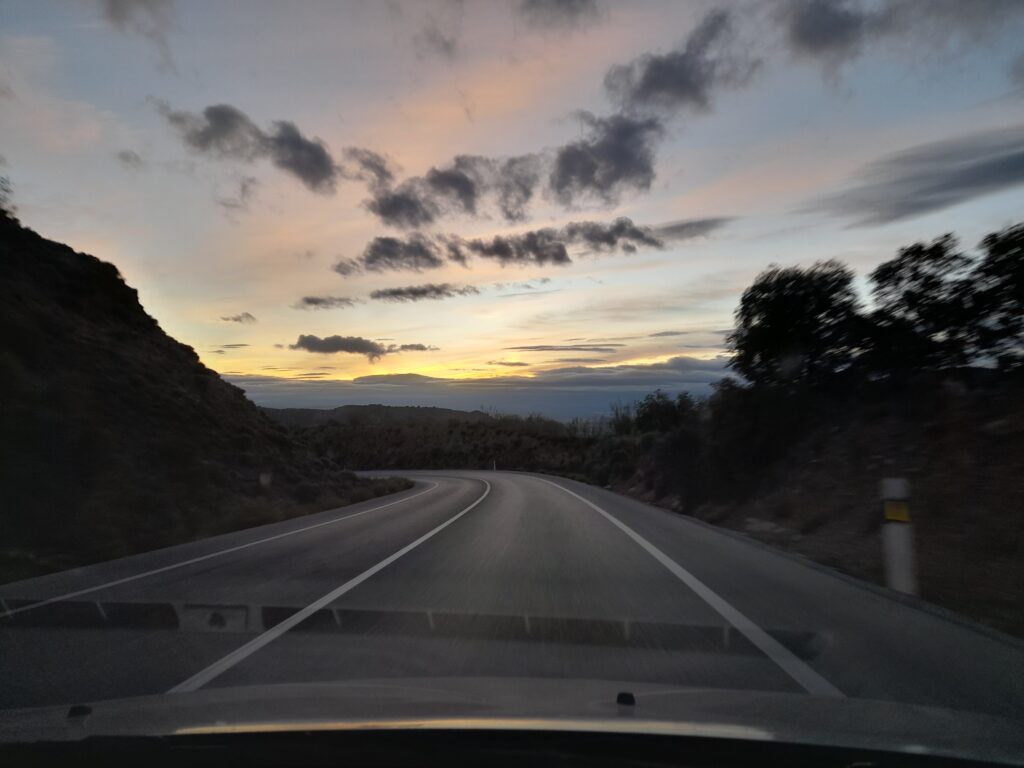
Team LRW’s latest HET trip, and why you need a jumper in Granada
Hot environment testing (HET) and hot-altitude testing (HAT) are a core part of LRW’s testing services. Ensuring new vehicles perform in all environmental conditions – including extreme heat and altitude is a critical part of creating all prototypes. Testing usually occurs outside of the UK, in Europe, to fully test performance in different ambient pressures. Why environmental testing? To ensure any new powertrain or variant is fully tested in hot, high and cold environments To understand the normal parameters as a standard part of the calibration testing process Testing in the field can be more effective than that using a climatic chamber as a broader range of road conditions, temperatures and pressures can be tested - which are not easily simulated Locations such as Granada are ideal as it is possible to efficiently test at sea level and altitude in one location How we tested The trip objectives were for the vehicles to be taken through the LRW standard test and validation plan to ensure that the diagnostics are stable in the following environments: At 35 degrees and above At ambient conditions At high altitude By changing one variable at a time, the team can identify how the engine performs in different temperatures and at high altitudes, where there will be less oxygen, lower ambient pressure and air density. The trip test team The testing team was made up of two senior engineers - Steven Higginson, Director, and Kristof Pawluc plus the ‘two Michaels - calibration engineers Michael Leech and Michael Horsnell: ‘Kris and I are hardened test trip guys, but it is still pretty epic to be driving luxury cars through such awesome scenery. It was the first LRW field trip for the Michaels, so it was brilliant to be able to introduce them to our field testing best practice - we were also delighted to discover that Michael H spoke fluent Spanish!’ So, any learnings for the LRW field-test newbies? The team were delighted with the trip and ‘the Michaels’ relished the field excursion but there was one learning, as Steven explains: ‘Whilst it’s around 35 degrees at the base of the mountains, it is very cold at the top. I looked ‘round when we reached the summit to see a slightly blue Michael Leech in t-shirt and shorts. I think the guys will now always remember to take a jumper!’ Trip outcome The diagnostics performed as expected and were stable in all conditions. Calibration updates were delivered to the OEM client to ensure robust diagnostics in hot and high conditions. Next up? Cold testing season in January when the team typically head to Austria or Sweden, so the team will definitely need a jumper for that one! Need support with environmental testing? Get in touch with the team at [email protected].
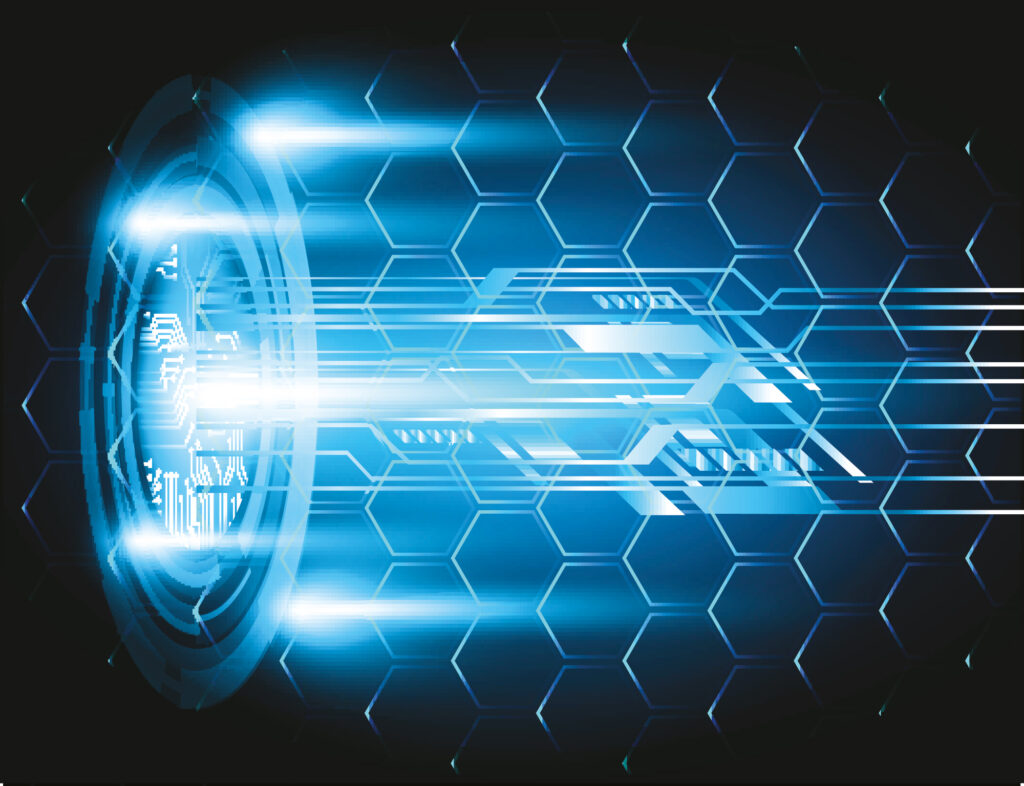
LRW Engineering Associates supports development of hydrogen-electric powertrain for passenger aircraft
Project overview The client needed additional headcount to develop a new disruptive technology powertrain with a hydrogen-electric engine, designed to support small passenger aircraft. LRW were selected because of the team’s specialist powertrain and hydrogen fuel cell expertise. LRW Engineering Associates services LRW provided 2 full time equivalent (FTE) Senior Engineers to support the client’s engineering team for 3 months working on the hydrogen-electric powertrain project. Key areas of focus for the project included: - Fuel cell control system design and development support - Fuel cell diagnostic system strategy consultation and software design ‘We were delighted to support this exciting new energy project. Our specialist knowledge means that we could make a real impact for the client fast and I’m pleased to say that the project has been extended so we can continue to support the client’s engineering team with debugging controls and testing. Our ethos is to work as a true extension of the in-house team and the project feedback has been extremely positive.’ Richard Threlfall, LRW Engineering Associates Director - New Energy & Integration Outcome By using LRW’s experience, the client has been able to progress the control system development and diagnostics more quickly – without the need for hiring additional permanent staff. It has also enabled the client project team to remain on track to meet the certification timeline. Got a project in mind? Get in touch at [email protected] to see how we can help.
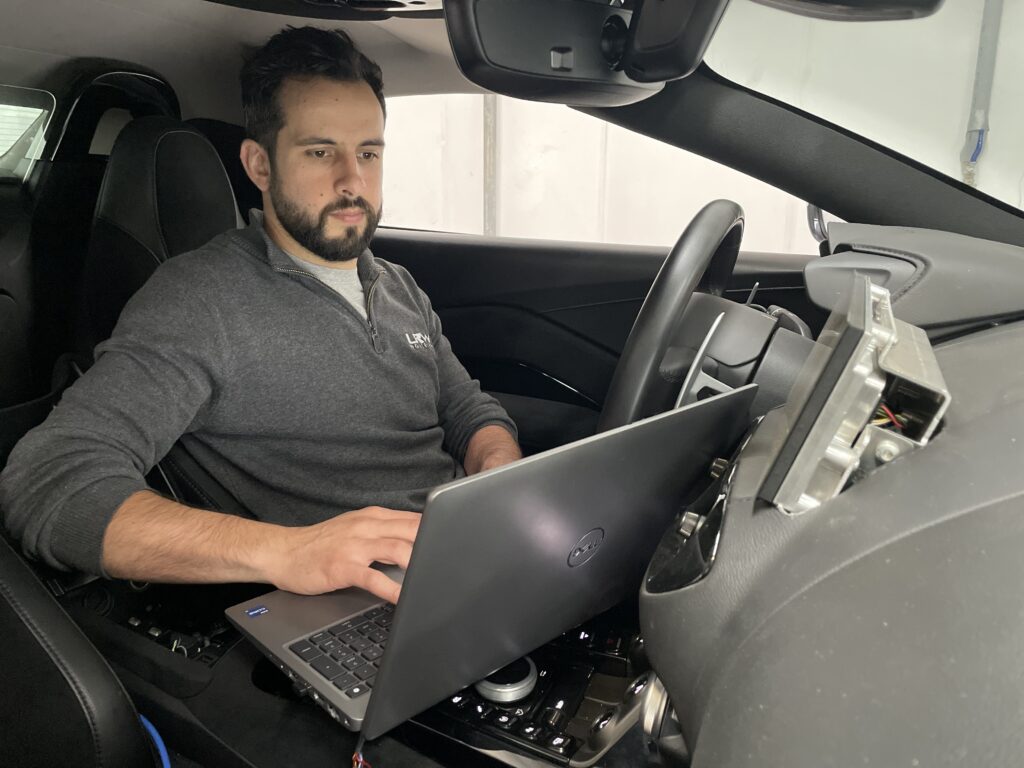
New director appointed at LRW Engineering Associates Ltd
LRW Engineering Associates, the engineering powertrain consultancy, are pleased to announce that Jared Al-Hilali has been appointed a director and partner of the business, commencing May 2023. Jared has strong ties to LRW as he worked for the business for five years from 2014 to 2019, re-joining in April last year as a Calibration Engineer. Jared has impressive engineering credentials built over a 10-year career which includes working for Group Lotus, Robert Bosch Engineering and Nissan Motor Manufacturing. Appointing Jared is a key part of the Director’s plans to significantly grow the business over the next four years. Commenting on the appointment, LRW Director Richard Threlfall said: ‘The LRW leadership team are delighted to welcome Jared onboard as a partner. Jared brings a wealth of experience from his previous roles and will be focused on the OBD calibration space as well as hydrogen fuel cell work. We’re looking forward to working with him and we’re really excited about the future of LRW.’ On becoming an LRW partner, Jared commented: ‘I’m delighted to have joined LRW as a director at this exciting time. There is so much potential for the business and we know that many automotive and aerospace manufacturers will be looking to outsource as their engineering teams become increasingly stretched as the focus moves towards new energy. I’m looking forward to working with the team and growing the business together.’ LRW Engineering Associates continues to grow with 3 new employees joining the business in the last year. As part of the expansion, the directors are always interested to hear from great engineering talent - so please get in touch.
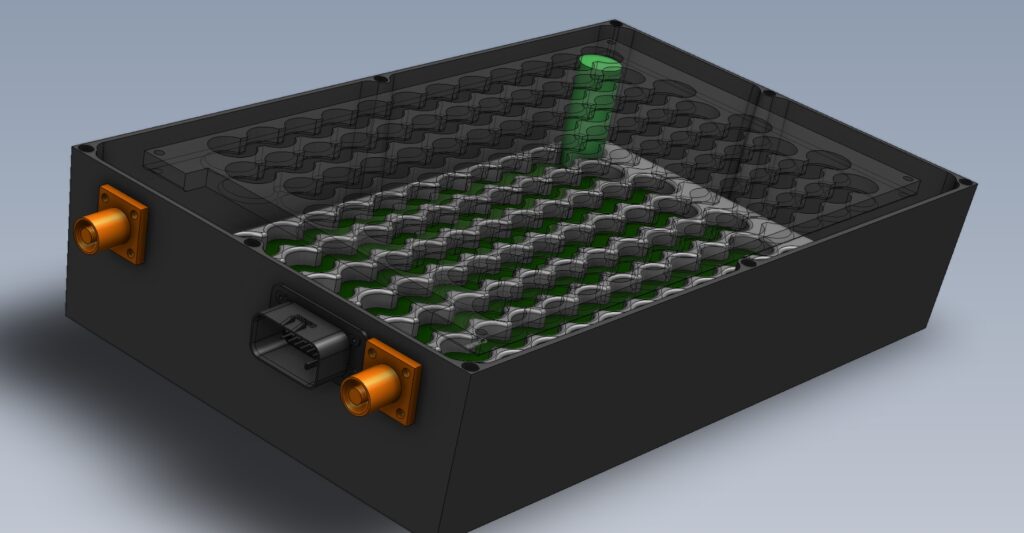
LRW Engineering Associates harnesses machine learning
There is a need to improve Battery Management Systems (BMS) in the aerospace industry and other sectors which use electrical propulsion systems. Batteries degrade with use, so being able to accurately estimate battery state of health (SoH), the useful life of a battery, is crucial. This is particularly important as we transition to a greener future because efficient battery technology is critical across all electric vehicles and renewable energy systems. Traditional methods of estimating battery SoH rely on mathematical models and physical measurements which can be complex and time intensive. Currently, ways of measuring SoH are pessimistic, meaning batteries are discarded although they may still be viable. Research approach LRW Engineering Associates and Warwick Control Technologies wanted to explore whether machine learning (ML) could simplify and improve the SoH process to optimise battery usage, life, and performance - and also improve BMS security. The businesses successfully secured a project grant through Aerospace UP – an organisation set up to support the Midlands aerospace supply chain to develop innovative technologies. Project team A project team was set up which comprised: LRW Engineering Associates – specialising in battery diagnostics and prognostics Warwick Control Technologies - focused on BMS cyber security ORKA Group - providing the fabrication of the moulded battery case Objectives LRW were focused on 2 key project objectives: To work towards establishing an improved BMS system - which combines innovative and cost-efficient SOH monitoring capabilities. To work with ORKA to create a re-usable casing for batteries to decrease current wastage – typically batteries are sealed within a unit which is then discarded at end of life. Project methodology The project was designed to run over a 20-week period. LRW developed a best practise methodology for the BMS SoH project covering 6 key stages: 1. Data Collection A diverse set of battery data were collected, including voltage, current, temperature, and other key parameters. Each SoH module was assembled into the same re-usable enclosure and run through an identical series of tests. 2. Feature Extraction Relevant features were extracted from the collected data that captures the battery's behaviour. The approach was limited to steady-state discharge profile only. An initial characteristic was established by conducting a slow discharge, further discharge profiles were conducted, and features were post processed. 3. Training Data The collected data were divided into training and testing datasets. The training dataset was used to teach the machine learning model the relationship between the extracted features and the SoH values. A small amount of training data were used on all available regression algorithms to select the best 5. 4. Model Selection The Matlab Regression Learner App was deployed for this process. LRW selected the most appropriate machine learning algorithms which included TFT Tree: Fine Tree, EBT Ensemble: Bagged Trees & SFG SVM: Fine Gaussian SVM. The training data were then applied to each of these 5 learning routines and results compared. 5. Model Evaluation The trained model's performance was assessed to measure the model's predictive capability using the testing dataset against metrics such as accuracy, mean absolute error, or root mean square error. The best ML result was 75% accuracy using the Fine Tree regression learning algorithm, 2 models were discarded. 6. SoH Prediction Once the model is trained and validated, it can be used to predict the SoH of a new battery. The battery's operational data are fed into the model, which then generates an estimate of the battery's SoH. Outcome The preliminary outcomes were successfully achieved and demonstrate that it is feasible to use machine learning for calculating battery SoH. This means it will be possible to enhance the management and performance of batteries in a wide range of applications, leading to more efficient and sustainable energy systems. The overall project has successfully delivered 3 new pieces of intellectual property: A 75% accurate battery SoH development process and algorithm based on machine learning. A re-usable battery module design that can take used lithium battery cells - This new unit design will provide safe battery storage and could be used and sold for multiple applications -including storing solar energy within workplaces or residential homes. A cybersecure CAN bus demonstrator which will show the capability of technologies for network intruder detection – a patent is currently under application by Warwick Control Technologies. The project team has plans for a further grant application to refine the machine learning iterations. It is anticipated that these capabilities will lead to meaningful developments within the aerospace and electric vehicle sector through collaboration with manufacturers. ‘We’re delighted with the project outcome and it’s great news - not just for aerospace, but for all sectors that use electrical propulsion systems. Ultimately, better battery management and more accurate diagnostics and prognostics means we can reduce the battery lifecycle and wastage. We’ll be able to refine our approach further as we go into the next phase of the research.’ Richard Threlfall, Director, LRW Engineering Got a project in mind? Get in touch to see how we can help.